Trans Brace
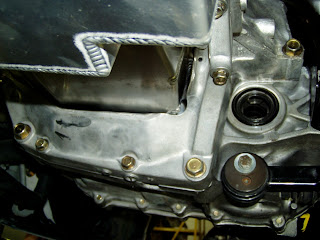
I believe in maximizing the rigidity of the block / transmission assembly. We had to reconfigure Honda's brace to fit properly with the Moroso oil pan. Details like this are important to building a long-lasting combination.
Engine 2stoke,4stoke and many more guide line